Comprehensive Pipeline Welding Inspection Solutions for Industrial Projects
Wiki Article
Crucial Pipeline Welding Inspection Tips for Quality Assurance
How can one assure the top quality of these welds that link the pipeline areas? By understanding the important pipe welding examination suggestions, experts can prevent possible hazards, decrease expensive fixings, and promote the dependability of these critical frameworks.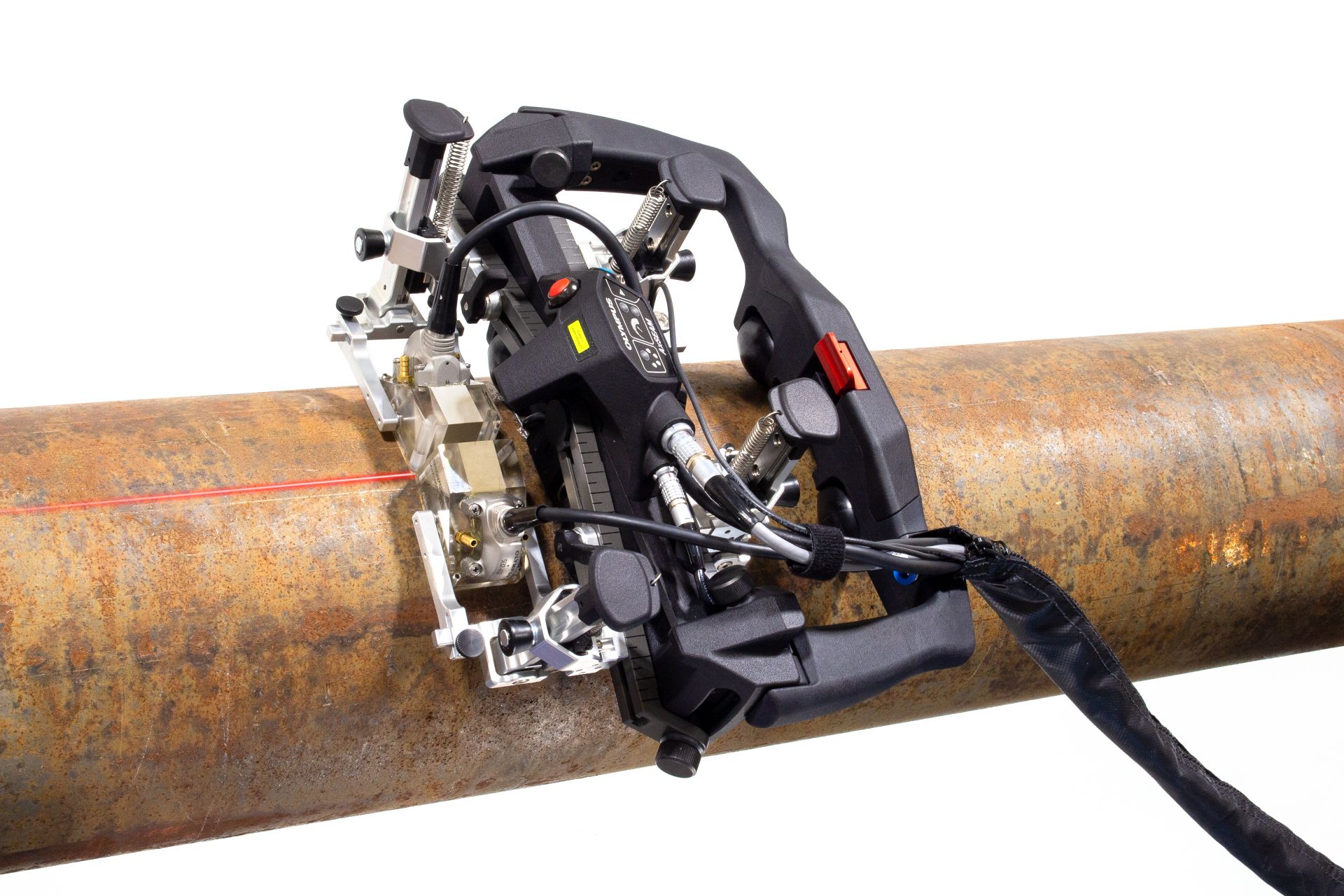
Significance of Welding Examination
Welding inspection plays an essential function in making sure the architectural integrity and safety and security of pipeline systems. By diligently checking out welds, examiners can identify any kind of flaws or blemishes that might jeopardize the honesty of the pipe. These inspections are essential for avoiding leakages, tears, and other possibly tragic failures that might result in ecological damages, economic losses, and even death.The importance of welding assessment can not be overemphasized, as the high quality of welds straight impacts the general performance and long life of the pipeline. Through non-destructive testing techniques such as aesthetic examination, ultrasonic screening, radiography, and magnetic fragment testing, examiners can identify imperfections that may not show up to the naked eye. By identifying and resolving these concerns early on, welding evaluation aids to ensure that pipes satisfy sector standards and regulative needs.
Inevitably, welding assessment is a crucial aspect of quality guarantee in pipeline maintenance, construction, and repair (Pipeline Welding Inspection). By upholding rigorous examination criteria, industry experts can mitigate risks and support the safety and reliability of pipeline systems
Common Welding Defects
Amongst the challenges encountered in pipeline welding, typical flaws can substantially impact the architectural stability and efficiency of the bonded joints. Splits in the weld can circulate over time, jeopardizing the architectural stability of the pipeline. Detecting and dealing with these common defects via comprehensive evaluation and quality control procedures are necessary for guaranteeing the reliability and safety of pipe welds.Examination Strategies for Pipelines
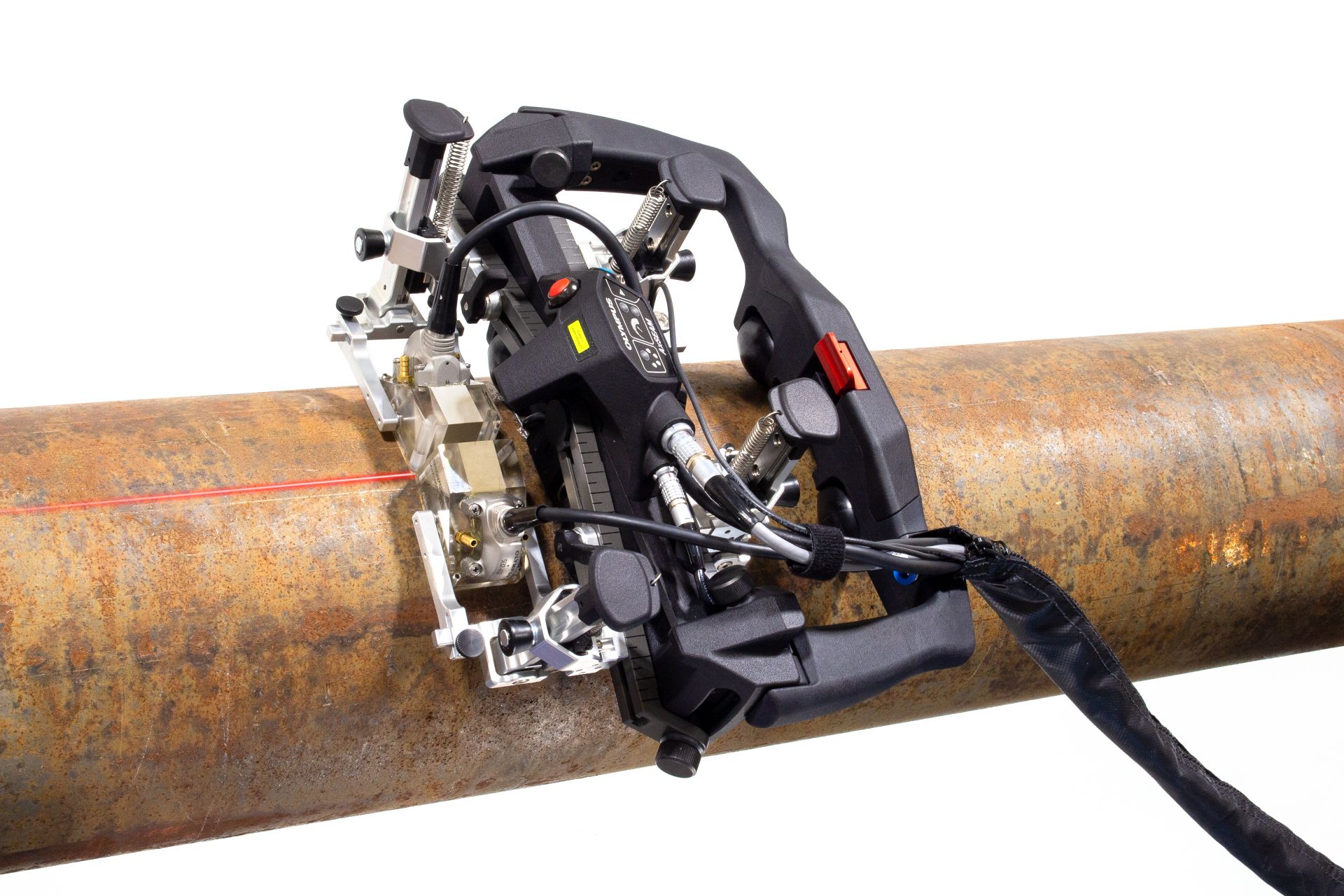

Non-destructive screening (NDT) strategies such as radiographic testing, ultrasonic testing, magnetic particle screening, and liquid penetrant testing are commonly utilized in pipe welding evaluation. Aesthetic inspection is likewise crucial in pipeline welding to determine any kind of noticeable problems or stoppages. Furthermore, automatic inspection techniques making use of innovative innovations like drones and robotics are significantly being utilized to improve the performance and accuracy of pipe assessments.
Guaranteeing Quality Control Requirements
To promote strict quality control standards in pipe building and construction, precise adherence to developed market procedures and standards is crucial. Quality guarantee in welding processes calls for a comprehensive technique incorporating numerous stages of pipe building. Making sure the quality of welds involves making use of qualified welders, proper welding treatments, and adherence to sector standards such as those established by the American Petroleum Institute (API) and the American Society of Mechanical Engineers explanation (ASME) Assessment and screening play a vital role in validating the integrity of welds, with methods like non-destructive screening (NDT) being critical for detecting possible flaws. Furthermore, maintaining in-depth documentation throughout the welding procedure is crucial for traceability and quality assurance functions. Applying a robust top quality administration system that consists of routine audits and reviews can additionally boost the overall quality control requirements in pipeline welding. By prioritizing adherence to these standards, stakeholders can ensure the reliability and safety of pipe systems for the lengthy term.Preventing Pricey Repair Work
Given the vital significance of maintaining rigid high quality guarantee criteria in pipeline building and construction, an aggressive approach to stopping costly repairs is necessary. Regular upkeep checks click to find out more and surveillance of ecological aspects that might influence the integrity of the pipe are also essential in protecting against costly repairs. By investing in preventative actions and focusing on top quality assurance at every stage of the pipe welding procedure, companies can decrease the threat of costly repair services and ensure the long-term integrity of their framework.
Verdict
In verdict, adherence to appropriate welding evaluation methods is crucial for ensuring the top quality and integrity of pipes. By identifying common welding flaws and carrying out detailed assessment procedures, costly repair services can be protected against, and quality control requirements can be fulfilled - Pipeline Welding Inspection. It is important for pipe welders to prioritize examination treatments to maintain the safety and security and integrity of the framework they are dealing withThe significance of welding assessment can not be overstated, as the high quality of welds directly impacts the overall efficiency and long life of the pipeline. Non-destructive screening (NDT) methods such as radiographic screening, ultrasonic testing, magnetic particle testing, and fluid penetrant screening are typically used in pipeline welding examination. Aesthetic examination is likewise vital in pipeline see it here welding to recognize any noticeable defects or interruptions. Furthermore, computerized evaluation methods utilizing innovative technologies like robotics and drones are progressively being utilized to improve the performance and precision of pipe assessments.In conclusion, adherence to correct welding examination methods is essential for making certain the high quality and stability of pipelines.
Report this wiki page